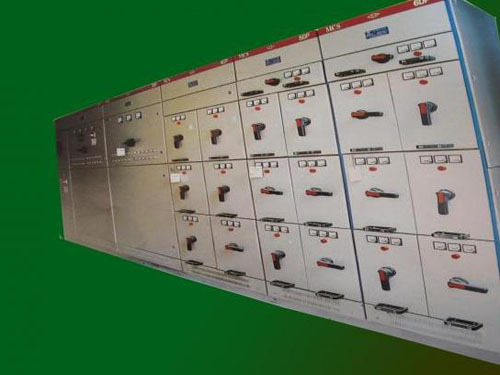
In recent years, the prices of core materials and conductive materials used in electronic transformers in power supplies have continued to rise, and upstream raw materials have formed a seller’s market. As a power supply user of downstream electronic transformers, they can select and purchase globally to form a buyer's market. In the middle of the electronic transformer industry, only take the road of technological innovation to get rid of this dilemma. However, in the mature electronic transformer industry, technological innovation is more difficult. However, the improvement of every small link can bring new ideas and new products. Therefore, this article introduces new developments of electronic transformers in power supplies in recent years from new materials, new structures, new principles, and new products. For readers' reference, if anything, please correct me.
To take the road of technological innovation, we must always remember the purpose to be achieved. The electronic transformer in the power supply, like any product that is a commodity, carries out any technological innovation, and must complete specific functions under specific conditions of use. The pursuit of performance is the best price. Today's power supply products are generally characterized by "lightness, thinness, shortness, and smallness," and are becoming smaller and portable. The electronic transformer must adapt to the volume and weight requirements of the user's power supply product. At the same time, the prices of raw materials (core materials and conductive materials) for electronic transformers have risen. Therefore, how to reduce the volume and weight and how to reduce the cost has become the main direction for the development of electronic transformers in recent years.
1 new material
1.1 Silicon Steel
Silicon steel is a massive use of electronic transformers in industrial frequency power supplies
Iron core material. To reduce the amount of iron used in an electronic transformer, the working flux density (working magnetic density) of silicon steel must be increased. The working magnetic density of silicon steel is determined by both the saturation flux density and the loss. Because efficiency is an important performance indicator for electronic transformers, many power supply products now offer standby loss requirements in order to save energy. The core loss of the electronic transformer is the main component of the standby loss. Therefore, all of them require clear and strict requirements on the efficiency or loss of the electronic transformer.
In recent years, the prices of oriented and non-oriented cold-rolled silicon steels have risen. Compared with R-type, CD-type, and EI-type cores, roll-type annular cores can save more than 20% of the cost of core materials and expand electronics compared to R-type, CD-type, and EI-type cores. The scope of use in the transformer. The wound-type toroidal core can give full play to the properties of oriented cold-rolled silicon steel, and its working magnetic flux density is much higher than that of non-oriented cold-rolled steel. At the same time, unlike the R, CD, and EI iron cores, silicon steel materials can be fully utilized with no corner scrap and a material utilization rate of more than 98%.
In recent years, there have been considerable improvements in cold rolled oriented silicon steels. The 23Q110 0.23mm oriented cold-rolled silicon steel has a unit weight loss of 1.10 W/kg at a working flux density of 1.7 T and 50 Hz. The 0.23 mm thickness of cold rolled silicon steel P1.7/50 is 0.88 W. /kg.Tension coating after surface treatment of silicon steel strip, P1.7/50 drops to 0.7W/kg. Change annealing process, refine magnetic domain, P1.7/50 then drop to 0.55~0.45W/kg, Far less than 0.35mm thick non-oriented cold-rolled silicon steel at working magnetic density 1.5T and 50Hz (P1.5/50) 2W/kg. Under the same loss conditions, 0.23mm thickness cold-rolled silicon steel working magnetic density It can reach 1.85T. If it is selected to process the toroidal core, it will be 1.23 times higher than the working magnetic flux 1.5 T of non-oriented cold-rolled silicon steel, and the core cross section and volume can be reduced by more than 23%.
Nowadays, in the power adapters of mobile phone chargers and home appliances, the EI-type core power frequency power transformers are widely used, and overheating sometimes occurs. The EI type iron core is formed by EI-shaped punched sheets. One-fifth of the E-shaped punching sheets are orthogonal to the longitudinal direction (orientation direction). To withstand the transverse magnetic field, non-oriented cold-rolled silicon steel is generally used. In recent years, Kawasaki Corporation of Japan has developed RGE series oriented cold-rolled silicon steel for EI type cores, with a thickness of 0.35 mm, a longitudinal saturated magnetic density of 1.80 to 1.90 T, a transverse saturated magnetic density of 1.825 T, and a loss of P1.7/50. 1.10~1.25W/kg. At the same time, the insulating film is relatively thin, and the stamping processing performance is good. Using it to make the core, the working magnetic density is desirable to be more than 1.7T, which is 15% higher than that of non-oriented cold-rolled silicon steel, and the core cross section and volume can be reduced by 15 Above +%, the loss is also greatly reduced and no overheating will occur. Japanese Kawasaki Corporation also developed a non-oriented cold-rolled steel with high saturation magnetic density, thickness of 0.5mm, silicon content of less than 1%, 0.6%, aluminum content of 0.3%, plus 0.52% nickel, saturated magnetic density of 1.96T The loss P1.5/50 is 3W/kg. Using it as an EI core material, the working magnetic density is also desirable 1.7T, but the loss is large.
It is worth noting that: As a large class of power transformers of electronic transformers, after using core materials with high magnetic core density, it is possible to reduce the number of coil turns and reduce the amount of copper without reducing the core section and volume. In the present situation where the price of copper is much higher than that of iron core material, it may be a better design improvement plan.
1.2 Soft Ferrite
Soft ferrite is a core material used in a large number of electronic transformers in high-frequency and high-frequency power supplies. Compared with metal soft magnetic materials, soft ferrite has low saturation magnetization, low magnetic permeability, and low Curie temperature. Several major weaknesses. In particular, the Curie temperature is low, the saturated magnetic density Bs and the unit volume power loss Pcv will change with temperature. As the temperature rises, Bs drops, Pcv begins to fall, and rises after reaching the trough. Therefore, under high temperature conditions, as long as Bs maintains a high level, the working magnetic density Bm can be selected to be higher, thereby reducing the number of turns of the coil and reducing the amount of copper used and the cost. High-temperature, high-saturation, magnetically-encapsulated ferrite materials can also extend the upper limit of the temperature used by electronic transformers to 120 or even 150 angstroms. For example, in a high-frequency electronic transformer in an automotive electronic device, a high-temperature, high-saturation, magnetically-encapsulated soft ferrite must be used in a high-temperature condition where the external temperature conditions vary widely and the engine room heats up.
As a MnZn soft ferrite used in high-frequency electronic transformers, TDK Corporation of Japan represented the development process of PC30→PC40→PC44→PC50→PC47→PC95→PC90. At 100°C, 100kHz, 200mT test conditions, the power loss per unit volume continues to decrease. According to the data released by the company in April 2006, the PC30 is 600mW/cm3; the PC40 is 420mW/cm3; the PC44 is 340mW/cm3; the PC47 is 270mW/cm3. However, the saturation magnetic flux Bs at 100%, PC30, PC40 and PC44 are basically 390 mT, and PC47 is 410 mT, which is far from the theoretical value of 600 mT. It cannot be considered as a high-temperature, high-saturation, magnetically dense material.
In recent years, in order to compete with metal soft magnetic materials in the field of application of electronic transformers, a round of development of high-temperature, high-saturation, magnetically dense MnZn ferrite materials has taken off. In March 2003, FDK Corporation of Japan developed the 4H series of high temperature and high saturation magnetically dense materials. Among them, 4H45 and 4H47 have Bs of 520 mT and 530mT at 25°C, 450mT and 470mT at 100°C, respectively, but at 100°C, the power loss Pcv is relatively high at 450mW/cm3 and
650mW/cm3. Allegedly, FDK Corporation developed 4H50 materials under laboratory conditions. Bs is 490 mT at 100°C, but Pcv is quite large, 800mW/cm3. Japanese TDK Corporation developed PC90 material in September 2004. At 25°C, Bs is 540mT, Pcv is 680mW/cm3; at 100°C, Bs is 450mT, Pcv is 320mW/cm3, which is higher than 4H45 material level. TOKIN Corporation developed BH3 material with a Bs of 540 mT and a Pcv of 600 mW/cm3 at 25°C, and a Bs of 440 mT and a Pcv of 370 mW/cm3 at 100°C. NICERA developed BM30 material. At 25°C, Bs is 540 mT, Pcv is 720 mW/cm3; at 100°C, Bs is 450mT, and Pcv is 320mW/cm3. High-iron and low-zinc ferrite materials developed by Hitachi Metals, Bs at 25°C, It is 563 mT; at 560 mT at 100°C, it is basically constant, and 490 mT at 150°C, but at 100°C, 100 kHz, 200 mT test conditions, Pcv is 1700 mW/cm3, which is high and needs improvement.
A Fan Heater, also called a blow heater, is a heater that works by using a fan to pass air over a heat source. including ceramic PTC heating element, wire heating element, copper heating element.
normal fan heater is of/fan/1000w/2000w, with thermostat , overheat protection,tip-over switch protection.
Fan Heater
Heater Blower,Electric Fan Heater,Room Heater Blower,Bathroom Fan Heater
Fenry manufacturing Co., Ltd , https://www.cnfenry.com