“We developed a steering reaction simulation system with complex algorithms using NI CompactRIO hardware and NI LabVIEW software in just two months.â€
This article refers to the address: http://
challenge:
Develop a steering reaction simulation system that collects data from different sensors, performs calculations, matches information, and produces output, and reliably executes a series of real-time tasks that require fast response.
solution:
Develop a steering algorithm simulation system based on complex algorithms in just two months using NI CompactRIO hardware and NI LabVIEW software.
The simulation of steering reaction during driving has been dynamic, as it depends on vehicle speed, steering angle and road conditions. In addition, the simulation system must also have a fast response time to generate reaction forces through the components.
Based on the data of vehicle speed, steering angle and steering angle acceleration, we obtained the steering torque data map and calculated the final reaction force based on this figure. We then pass these values ​​to a hydraulic system to simulate the final reaction. We design system logic to obtain data from different sensors, calculate data, match map data, generate output, and perform a series of real-time tasks reliably and quickly.
System Overview
We chose LabVIEW and CompactRIO to create our system. We chose the scalable 8-slot NI cRIO-9116 chassis. It has a Xilinx Virtex-5 Field Programmable Gate Array (FPGA) to help implement control logic and ensure fast response times. We also chose NI's cRIO-9024 real-time controller with a real-time operating system (VxWorks).
The cRIO-9024 controller has 4 GB of storage, 512 MB of DRAM and 800 MHz of CPU, which will help to capture, record and process large amounts of data quickly. In addition, with two Ethernet ports and one RS232 interface, the system can be easily connected to external devices. The USB port can be easily used to extend external memory media.
We used two 4-channel NI9215 analog input modules to process eight analog sensor signals. A 2-port NI9853 Controller Area Network (CAN) module is used for CAN communication with the Electronic Stability Program (ESP) Electronic Control Unit (ECU) under development.
We use the NI9474 module to generate eight digital outputs as pulse width modulation (PWM) signals to simulate vehicle speed. This PWM signal is then sent to the EPS ECU to virtualize a vehicle. This signal uses an isolated NI9269 module for analog signal output, eliminating interference between signals to ensure that the analog output for the hydraulic system is accurate enough.
In addition to precise control of digital and analog outputs, the CompactRIO configuration simulates dynamically changing sensor signals and CAN signals (a vehicle communication signal) in a vehicle. We created a fast and highly reliable vehicle simulation system using FPGAs and real-time operating systems.
Why do we choose NI products?
Considering that the system requires strict processing time accuracy, we need to achieve high-speed data acquisition, processing, and accurate digital and analog control signal output through FPGA. We also need real-time, dynamic control to realistically simulate the driving conditions of the vehicle, quickly calculate the data of the steering reverse torque of the vehicle, and build an embedded system that is not limited by the PC. LabVIEW reduces our software development time and provides a powerful library of functions to help us develop algorithms.
System Configuration
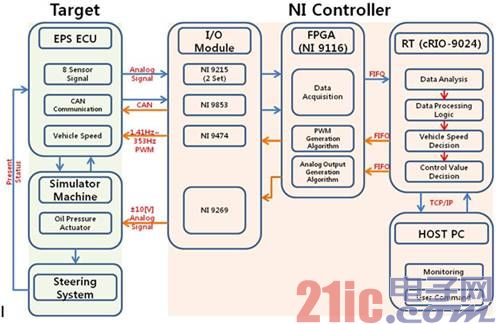
Figure 1: System Configuration
As shown in Figure 1, the 8-way sensor signal (NI9215) and the CAN communication data (NI9853) each receive a signal from their input object. The FPGA acquires signals from the EPS ECU with a sampling period of 100 μs and provides a vehicle speed signal (NI9269) using PWM waves (0 km/h to 250 km/h: 1.41 Hz to 353 Hz, duty cycle 50%) and finally transmits Give the EPS ECU.
Through the first-in, first-out (FIFO) mode, the collected data is analyzed and logically processed by the real-time processor (cRIO-9024) and converted to rms values. Then, in the real-time processor, the system uses a fast mapping algorithm (corresponding to the reaction force value of the standard map data store) to calculate the final control amount from the reference data and generate an analog output through an FPGA algorithm. The NI 9269 module provides control signals in the ±10 V range to the hydraulic actuator.
The input sensor signal and the final hydraulic system control value control the hydraulic system. They are also kept in the queue and then sent to the host PC via TCP/IP communication. This configuration allows the PC host to monitor the performance and status of the reaction simulator. In addition, the system provides the user with control over multiple signals while maintaining dynamic control.
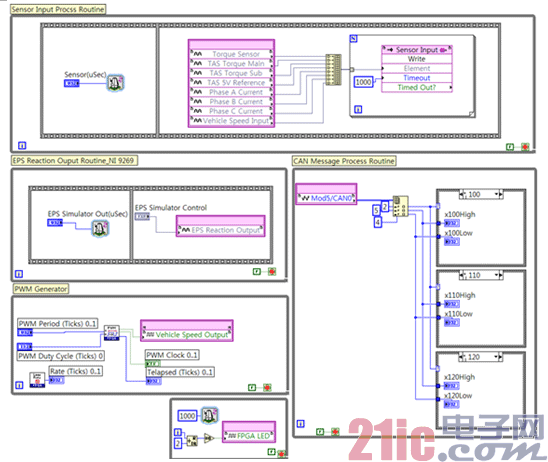
Figure 2: FPGA Block Diagram
Figure 2 shows the FPGA block diagram, the program for processing the sensor input signals and the program for handling messages for CAN communication. The EPS reaction force output program and the PWM generation program are respectively used to generate a control output signal of the hydraulic actuator and convert the vehicle speed into a PWM wave signal.
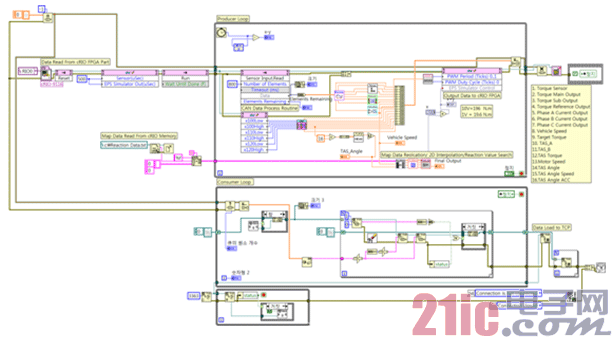
Figure 3 real-time block diagram
In Figure 3, the block diagram runs in the real-time operating system, data acquisition, FPGA output to obtain data from the database, and the final value is passed to the FPGA, and then the data is transmitted to the host via TCP/IP.
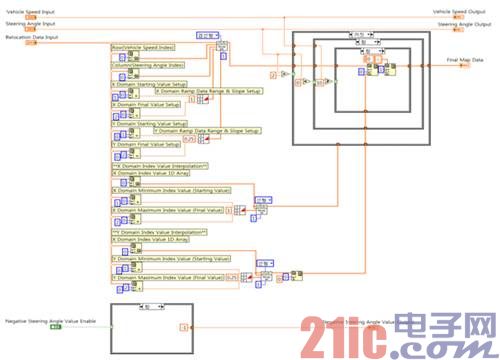
Figure 4 2D data interpolation block diagram
The most important part of the system is an algorithm that calculates different map data based on the standard values ​​collected from the sensors (see Figure 4). After subtracting the input reference information from the standard value, the data is reduced. To maintain linearity, the values ​​are extracted from the interpolation.
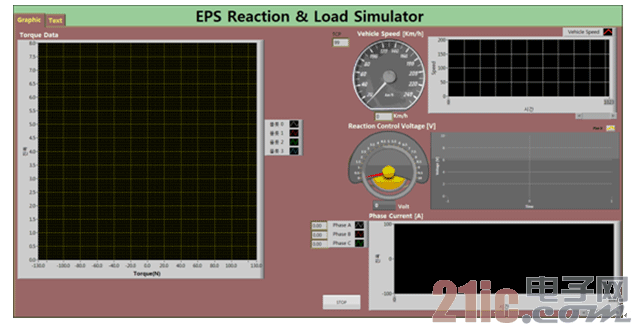
Figure 5: Main unit front panel
Figure 5 shows the host front panel for monitoring the state variables of the EPS simulator and different sensors. Most of the data shows historical values ​​on the chart, and important parameters are displayed separately.
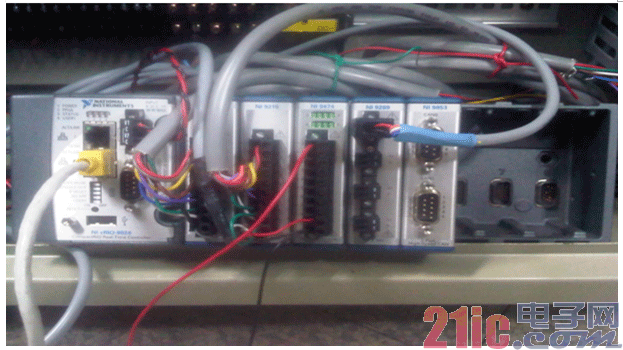
Figure 6: CompactRIO
in conclusion
We have 4 months to develop this app, but it was actually completed in just two months. We use LabVIEW programming to complete the fast function implementation and debugging of FPGA programs, which often requires a lot of time and experience. While deploying FPGA logic, we also implemented fast data acquisition.
The real-time operating system ensures highly secure and reliable data processing by using a proven operating system (VxWorks). Because the total cycle time of the target control is 50 milliseconds, this makes an efficient control effect possible. This is faster than providing the required response to the hydraulic actuator.
After the software is developed, it will be downloaded to CompactRIO for independent operation, and the reaction simulator will be smoothly controlled without PC control. By matching the vehicle-level reaction torque data, we can update the data in different driving conditions in the cRIO-9024 memory for more accurate laboratory-level simulation environment. Because of the scalability of the chassis slots, we can add more diverse vehicle driving conditions by adding one more module. This means we can use the original CompactRIO system design to adapt to new changes easily, cost-effectively and efficiently.
The biggest advantage of using LabVIEW and CompactRIO as a solution is that it can help us build complex algorithms quickly, easily, and accurately using simple combinations or simple variable changes.
With spiralling energy costs accompanying the constant need to replace bulbs and tubes our 2 ranges of Marine Aquarium Lighting makes perfect sense.A conservative savings in electricity consumption of up to 50% can be achieved over metal halides and 25% onT5 Fluorescents.
2 Manual dimmers for White, Blue change the intensity of lighting
Simulates the sunset and sunrise
55pcs 3w leds offer lighting to tank effectively
Adjustable kits, detachable cords
Philizon Lighting is dedicated to provide high quality and durable lighting product for customer with very competitive price.Our products mainly foucs on Led Grow Lights and Led Aquarium Light .The equipment and materials to produce Hydroponics Led Grow Light and marine Aquarium Led Light fixture imported from Taiwan, Japan, Korea and Unites States, such as automatic SMT machine, reflowsoldering machine,all kinds of electric test equipment, large integrating sphere and such sorts of productionand R&D equipment.
Item Display
Key Features
1.The lifespan is over 50000 hours,low maintenance costs.
2.Energy conservation,saving over 80% energy than the traditional HPS.
3.High light efficiency,90% of the light will be absorbed by the aquatic plants,while just 8%-10% to the HPS.
4.Build-in cooling system,could solve the heat dissipation excellently.
5.Built-in power supply, CE approved, No setup required, just simpler and safer plugs directly into AC85V-264V, no reflector & ballast needed.
Package Include
1 X LED Aquarium Light
1 X Free Hanging Kit
1X Free Power Cord
All the lamps have passed strict quality examination and are packed carefully before shipping.In order that our customers get high quality lamps,we attach importance to every details.
Application
1. coral reef lighting,fish tank lighting,coral reef tank lighting
2. Aquarium Lighting ,aquarium art,aquarium shop,aquarim centre
3. fish bowl lighting,fish lighting,freshwater lighting,saltwater lighting
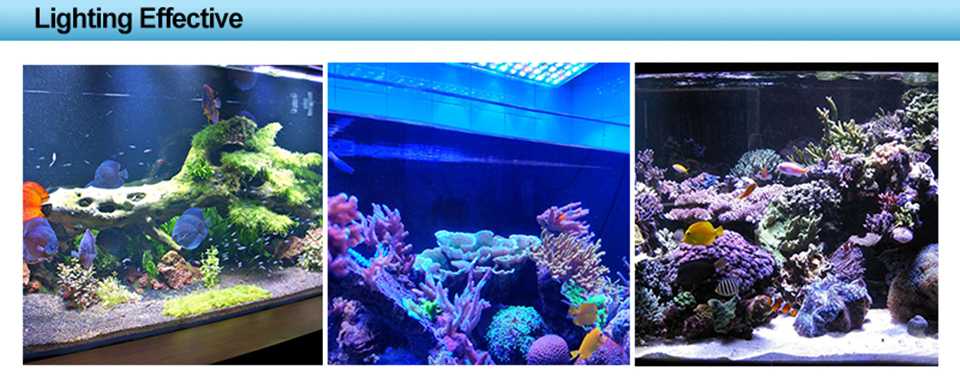
Our LED Plant Grow Light and led aquarium lamp are popular in led market,cause its elegant outlook and its high quality and competitive price.We are eager to kick off cooperation with you, our valuable customers. Let`s work together and save the energy.
Warmly welcome to visit Philizon in Shenzhen China.
Marine Aquarium Lighting
Marine Aquarium Lighting,Marine Led Aquarium Lighting,Marine Led Lighting,Marine Aquarium Led Lighting
Shenzhen Phlizon Technology Co.,Ltd. , https://www.philizon.com